By Sarah Porter
Bike frames line the wall of the Lost-Bikes workshop, arranged in chronological order from the first bike they ever made, to the most recent. Each one has been battered, beaten and muddied on local trails by company owners Eric Evans and Brian Davison.
Evans, a 28-year-old Western grad, works in the evenings at a laser cutting service called Cutters Inc., and spends much of his spare time working at the Lost-Bikes shop.
Davison, 27, is the production manager for a luxury car part company called Girodisc. Davison works at Girodisc during the day, and usually is at the Lost-Bikes shop in the afternoons.
Born in Evan’s garage, the Bellingham-based bike company is set to release their first small line of mountain bikes this March. Davison and Evans started the company by building bikes for themselves, and in 2016 they founded Lost-Bikes so they could build bikes for other people.

Evans and Davison are working on a new frame assembly method which could premier on the bike line. Instead of welding the aluminum frames, they want to connect the pieces with a special kind of glue.
“Really gnarly epoxy. Used for building airplane parts,” Evans said.
The full-suspension bike frame, called the Lost Lemonade, will retail at $2,500, according to their website. They are also working on a hardtail bike that could be market-ready just as soon.
Evans is planning on testing the glue method in the lab he used as a Western student studying plastics engineering technology. He used to work as an aerospace engineer for Janicki Industries, an engineering and manufacturing company based in Sedro-Woolley.
“We’re not generating garbage. We don’t have to worry about fumes, and all extra material is recycled.”
ERIC EVANS
Gluing is a common method for assembling carbon fiber bikes, but Evans said it has never been used to build aluminum bikes. It is less expensive and time consuming than welding, making it easier to produce a frame they think will be just as strong, he explained.
The only other company trying to manufacture bikes this way is Pole Bicycle Company, based in Finland, according to a press release from September.
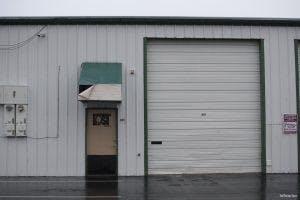
They are in a race with Pole Bicycle Company to be the first to glue aluminum frames, Evans said.
Made almost entirely in Bellingham with American metal, Lost-Bikes’ process produces less waste than carbon fibre, Evans said. The only part of the process they don’t do is the paint.
“We’re not generating garbage,” Evans said. “We don’t have to worry about fumes, and all extra material is recycled.”
Their bikes are cut from chunks of metal using a robotic machine that they bought off of eBay, and the leftover shards of metal are washed out and caught in a bin. Those shards can be melted down and recycled.
Another design element that sets them apart is the geometry — it stays proportional, no matter what size frame you buy. On most bike frames, only the length between the seat and the handlebars gets longer on larger frame sizes, Evans said. Lost-Bikes makes the whole frame larger.
