When senior Matt Hoogestraat sat beneath the elegant arches and high ceilings of Seattle’s Sanctuary Ballroom, he was nervous. It was here, in the country’s oldest byzantine-style building, he’d find out whether or not Western’s senior industrial design class had won the Gray Magazine award for best student design.
The award would recognize the students’ work on a project they completed at the end of their junior year titled Cube3. The ambitious project set out to address Bellingham’s affordable housing crisis by designing housing specifically for people living near the poverty level. Strangely enough, the project began early last spring as a simple chair.
“We were designing chairs as a small short-term project, and the idea was we were going to continue it into next year,” said Josh Pehrson, a senior in the industrial design program. “We started by asking the question, ‘What really is a chair?’”

From there, the students began to look at chairs from the perspective of the spaces they occupy, and the effect they have on our lives, Pehrson said. Soon enough, they were looking at housing as a whole, and the impact it has on our community. Eventually, they weren’t thinking of chairs at all, but of broader social issues in the context of our daily lives.
Their professor Arunas Oslapas was receptive to the idea.
“The students came to me and said, ‘We don’t want to do just a chair. We want to do something more meaningful, and we want to work as a team,’” Oslapas said.
Oslapas came to them with a newly designed prompt, one that asked them to address the housing crisis in Bellingham, and the students got to work.
They began by researching the issue exhaustively. The students talked to city development manager Rick Sepler, and scouted real locations around Bellingham where the housing could be located, Pehrson said. From the beginning, they wanted to be sure the project was grounded in reality.
“A lot of architectural concepts lack in that area,” Hoogestraat said. “We wanted to make this something that really was a manufacturable, feasible thing.”
The students each came back with their own concept to tackle the issue. The class took ideas from each, and compiled them into one fundamental blueprint to work off of.
They were then divided into teams that oversaw the interior, exterior, engineering and graphic design of the project, Hoogestraat said. Right away, the class ran into problems trying to keep things practical, minimal, and most importantly, affordable.
“It’s really easy to look at exotic solutions for mechanical problems,” Hoogestraat said. “But part of what we do in industrial design is come up with elegant solutions that are also minimal and simplistic, that don’t distract from the beauty of the design.”
The group ran into other challenges trying to condense different viewpoints into one cohesive project.
“You put 12 design students in a room, and I’m a designer too, we all have different opinions,” Oslapas said. “It’s extremely hard to get all of us to a unified decision.”
Pehrson saw it as an opportunity to learn to work collaboratively and make compromises on a professional level.
“It really came down to dropping the ego a little bit and just getting the work done,” Pehrson said.
In the end, they were left with a project that combined basic geometry and clever engineering to accommodate residents throughout the social spectrum. Ten-by-ten foot cubes acted as the housing’s frame, and inside was everything you need to survive, from sleeping quarters to living space. As the homeowner’s financial stability developed, or if they decided to start a family, additional 10-by-10 foot cubes could be added in all directions to expand on the existing residence.
Afterward, it was Hoogestraat that decided to submit the project to the Gray Magazine Awards judges.
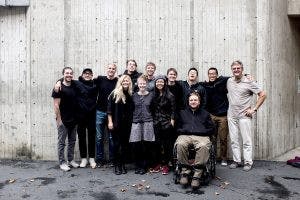
“I just thought it turned out really good,” Hoogestraat said. “I was excited about it and I didn’t want it to be finished after the show that year. I thought if we could get some more eyes on it it could be helpful to us, and maybe there’s potential for it to be taken further in the future.”
Months later, Hoogestraat’s class learned Cube3 had been selected as a finalist. They were invited to the magazine’s award ceremony in Seattle on Nov. 29, where they would announce the winner of each category.
The class entered the building in formal attire, as the invitation had requested, and found their seats in the enormous room. They were given a confetti cannon, and told to fire it if their entry won. The students took one look at the cannon and handed it to their professor.
Later, when the finalists for the student design category were announced, the students wriggled and twitched with anticipation. When the moderator announced that Western’s 2018 class of industrial design students had won the award, the professor fired the confetti cannon. A spotlight swiveled in their direction, and a waiter found them with a round of champagne. They had won.
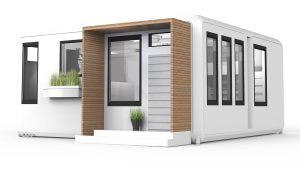
Of the 363 submissions the contest received, 51 went on to be finalists. Cube3 was one of 11 that won the final prize: a custom designed trophy and coverage in the December issue of Gray Magazine.
Judges for the contest included world-renowned designers, many of whom they’d studied in class. One judge, Philippe Starck, had designed the very building they were seated in.
Hoogestraat said the creation and celebration of the project brought his class closer together.
“Anytime you have to work together and struggle together it’s gonna bring you closer for sure,” Hoogestraat said. “We enjoyed working with each other and wanted to take it further and see what we could create as a group.”
As for where the project is at now, the students are just waiting for an investor or organization to take notice, so they can see it through to completion.
“I think it has a lot of potential,” Pehrson said. “But in context, it’s just a student project we did our junior year. We have a lot more in us than just that.”